RM Group
Mochdre Industrial Estate, Newtown
RM Group was founded in 1995 after leading a successful contract packaging operation for Trident Feeds. They provide contract packaging services to this day, alongside manufacturing bespoke packaging systems that are tailored to suit circumstance and budget.
RM Group supply and manufacture a wide range of manual & automated packaging machinery & systems. Including everything from Manual Bagging Machines, Robot Palletising Systems, Bulk filling and Material Handling systems, as well as supplying high speed Form Fill and Seal packaging lines and Horizontal Baling Machinery.
The company launched a mobile packaging system in 2005, after realising a demand to bag products at the source. This innovation sees greater flexibility as clients can pack products at the desired location, whilst dramatically reducing the time and cost of transportation.
One of the biggest and growing costs of operating this type of business is energy. Keeping the buildings heated to a good temperature year round for the steel working and storage temperature, and operating the large machinery including laser cutters uses a huge amount of energy each year. Reducing these energy costs is an easy way to make significant savings and make the operation much more profitable.
In order to reduce the consumption of expensive fossil fuel energy RM Group Founder and Director Edward Rees looked into the potential of biogas CHP. Working with our local partners ESP Energy, Edward undertook a process of due diligence. Visiting other local operational installations and understanding exactly how the system could be integrated into the site at Newtown.
The result was that a single arborElectrogen® 45 would be both a perfect fit to meet the site energy demands but importantly because of its compact nature, with a few modifications a suitable location was identified in an existing out building where the old oil tank was housed. Additionally, with an adjacent redundant water tank utilised for a woodchip fuel store the system was cleverly integrated without the need for any additional buildings.
In order to distribute the heat evenly around the factory 4 x 25kW space heaters were installed to provide an optimum working temperature in the workshop to maintain staff productivity. The electricity generated from the system is connected directly to the sites existing distribution board. Offsetting the vast majority of electricity that would have otherwise been imported from the grid. At times when the generation exceeds the onsite demands then the electricity is exported back to the grid.
Hand on heart go for it. Great bit of kit, love the software, and remote monitoring capability, makes a huge difference having those features
Other Case Studies
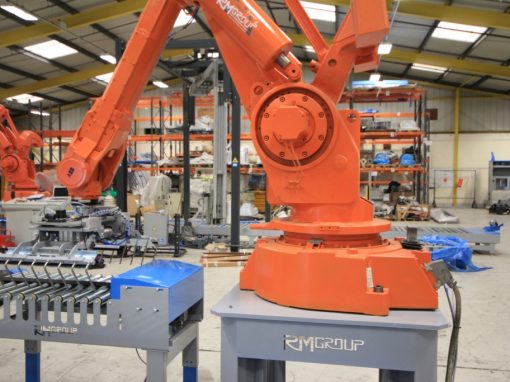
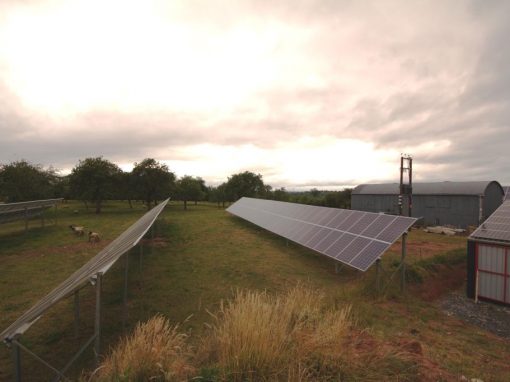
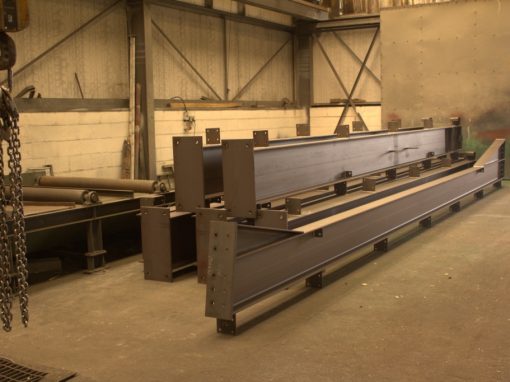
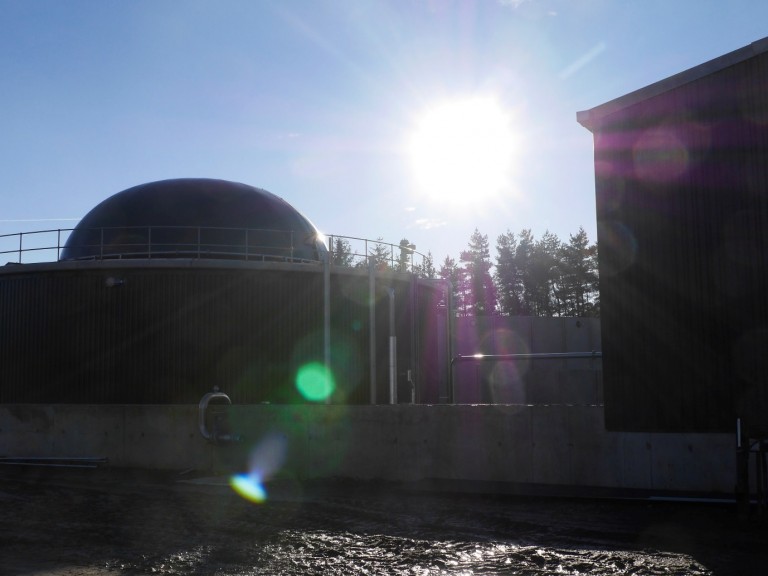
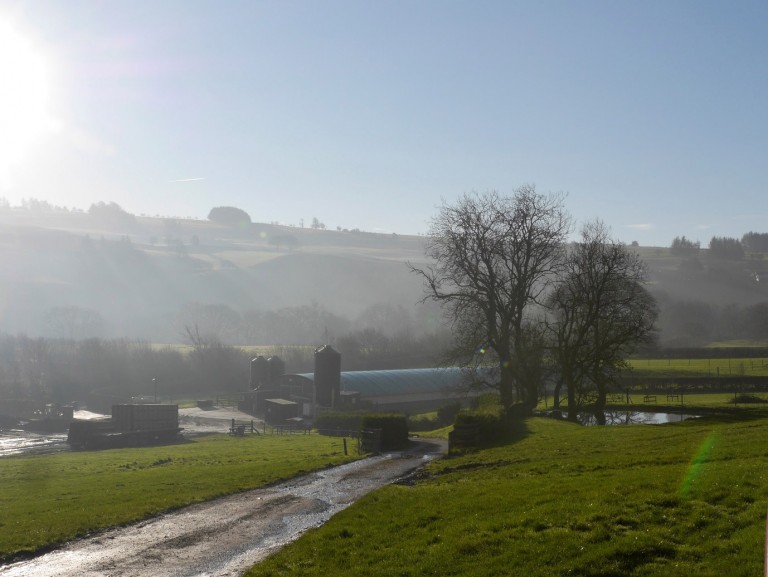
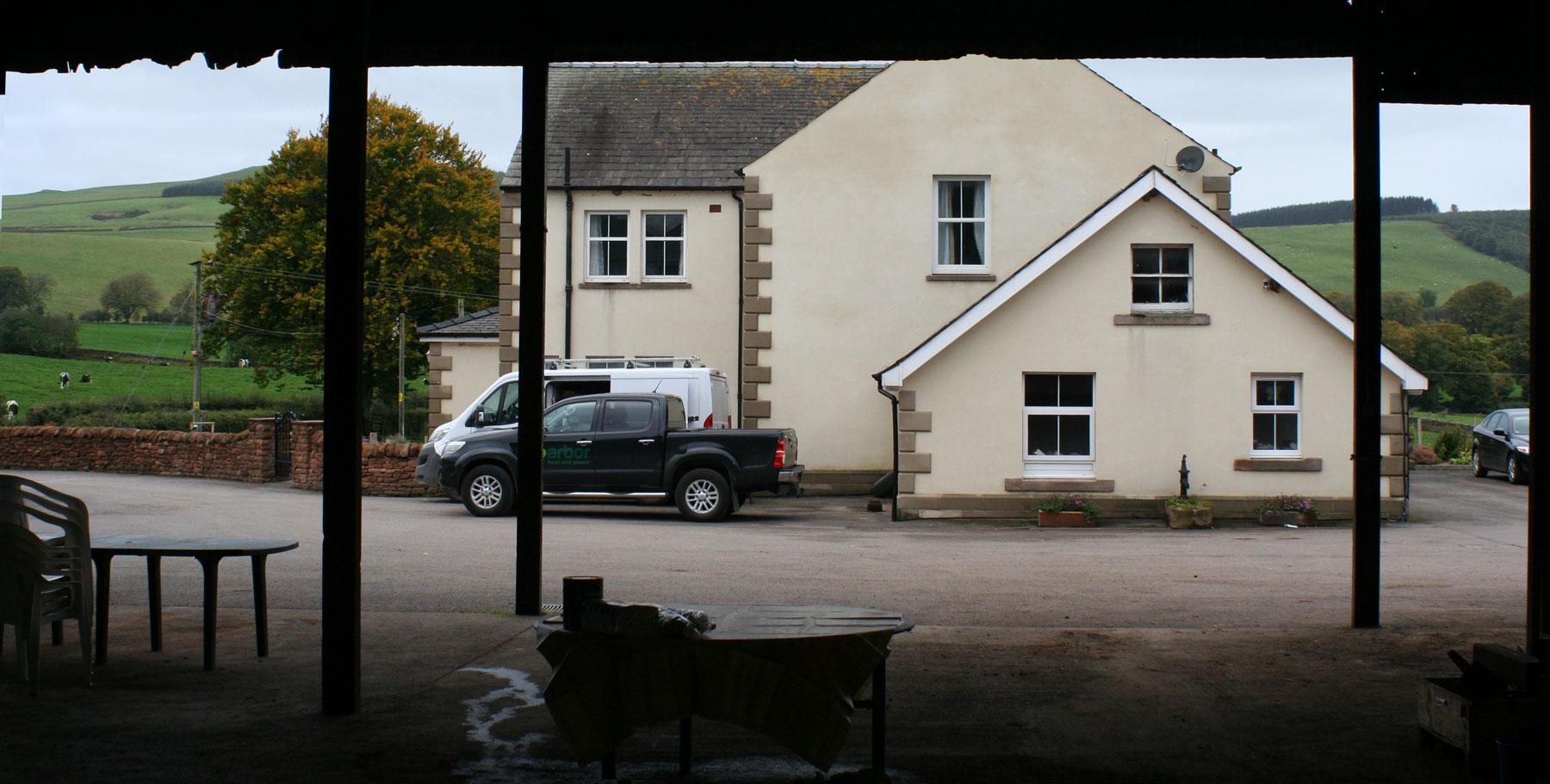
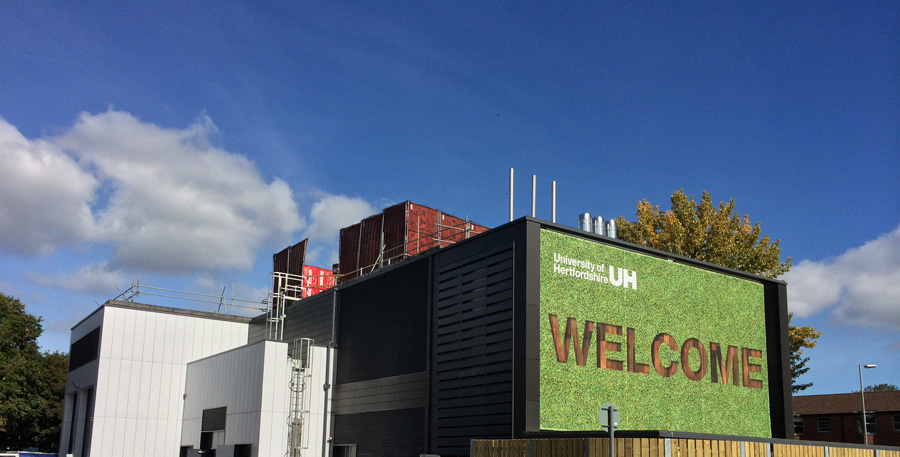
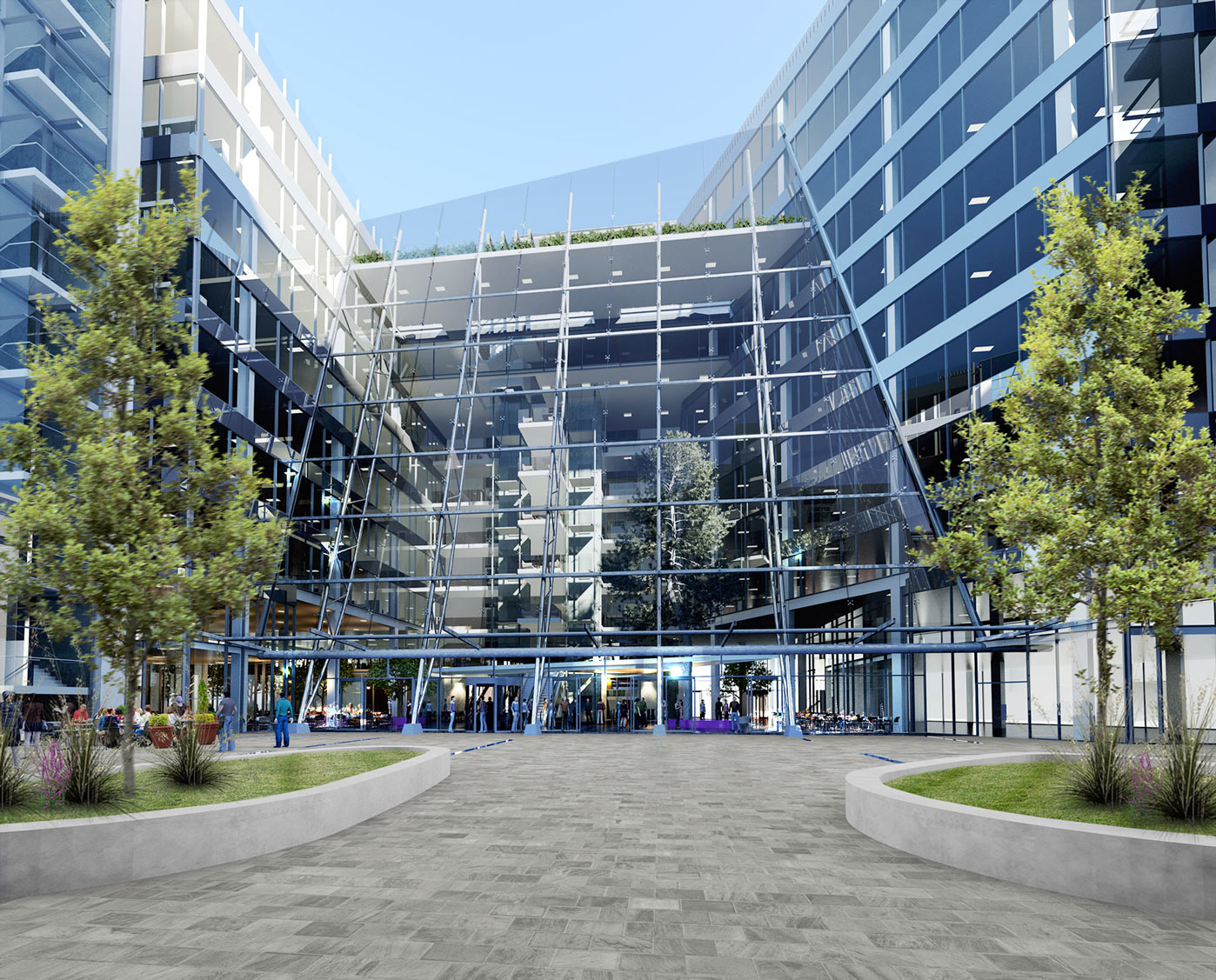
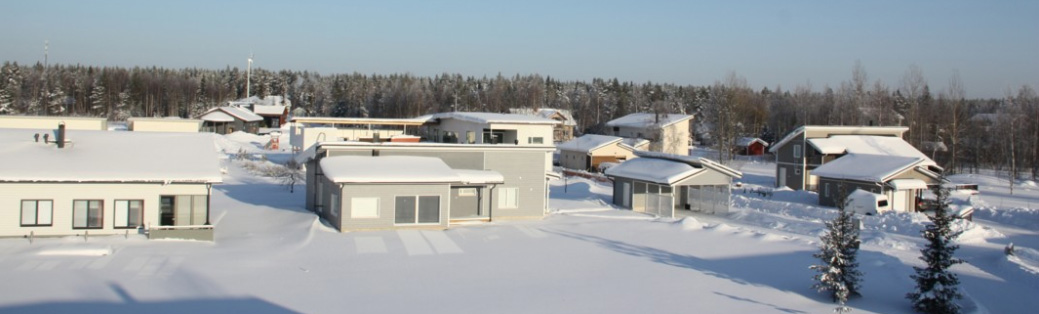