East Reston Farm
Ayton, Eyemouth
Father and Son, David and Pete Allan, are predominantly arable farmers and potato growers but also have a residential property development business. Situated North of Berwick-upon-Tweed, near Eyemouth, David and Pete’s business covers 2000 acres of arable farmland and 400 acres of potato land. With business energy usage rising and the company growing just as rapidly an alternative energy source was required to ensure that energy bills remained manageable. The pair wanted to make sure they had done their homework on which system would be right for them and took it upon themselves to travel through Europe looking at several different biogas CHP units.
Following the extensive research, the decision ultimately came down to an on-site constructed unit from Italy or the factory built arborElectroGen®. Working with the assistance of our Scottish distributors Mathers the decision was to select two arborElectrogen®45 systems. One of the key factors in the decision was the ease of installation and the pre-shipping factory testing that is undertaken on the arborElectroGen®. Both of which considerably cut down the installation and commissioning time on site that can be crucial to getting a system installed within a tight timescale.
For a large electricity user, it has to be the right thing to do
David Allan explains the decision to invest in the biogas CHP systems: The market for potatoes lasts 12 months of the year so being able to preserve them to release into the market at particular times is extremely important. To do this the potatoes are cooled to 2 degrees Celsius and stored in tonne box creates. When a gap in market appears the potatoes are removed from the cold store to be graded. However, to stop them bruising before they are graded they have to be warmed up to around 8 degrees Celsius this is where heat from the two arborElectroGen® systems comes in. Prior to the installation of this unit this ‘reheating’ process was using 1,000,000kWh a year of expensive fossil fuel.
As well as the potato processing, East Reston Farm use a drying floor to dry the grain from the 2000 acre farm. They were previously spending around £35,000 per year on diesel to fuel the drying floor. By installing a 500kW boiler and two arborElectroGen® units they were able to cut bills by two thirds.
Along with drying grain, they plan on drying their own wood fuel. By drying fuel onsite cost drops by approximately 50% for the two units. Consequently, along with this massive saving the excess chips will then be sold creating another valuable income.
Other Case Studies
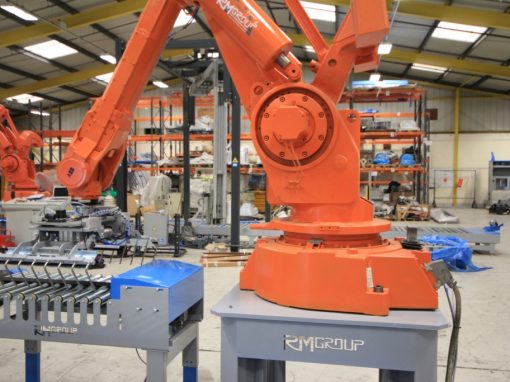
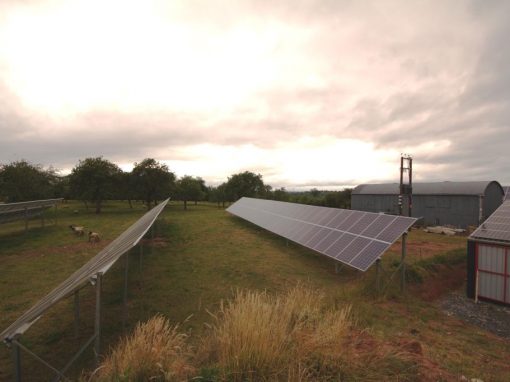
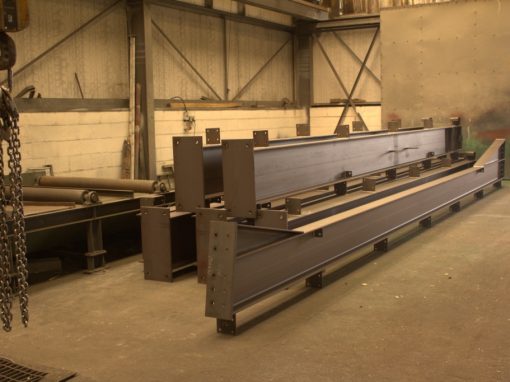
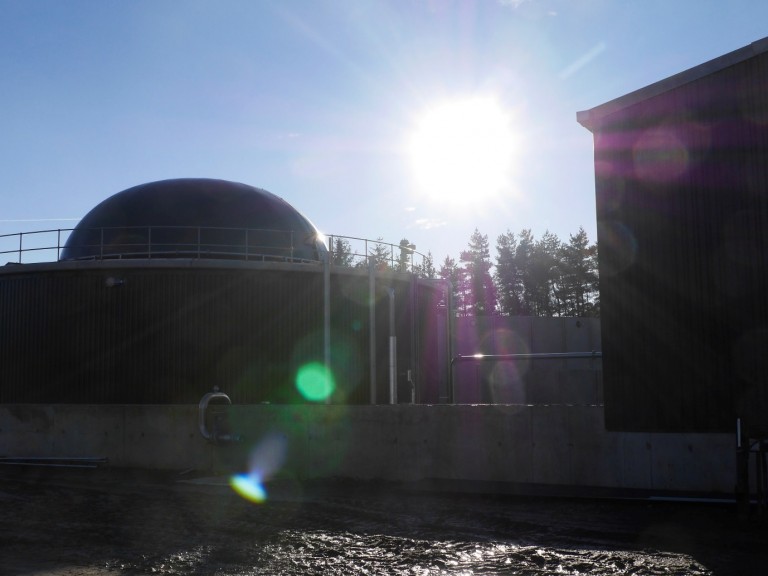
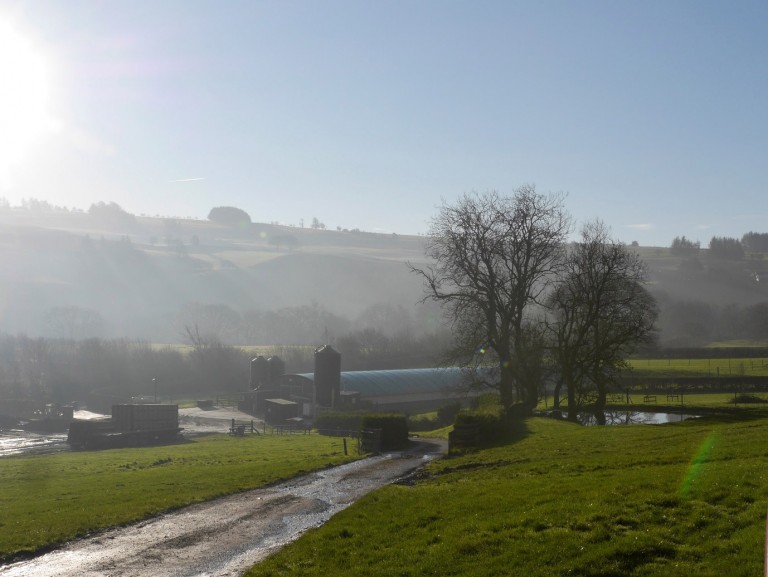
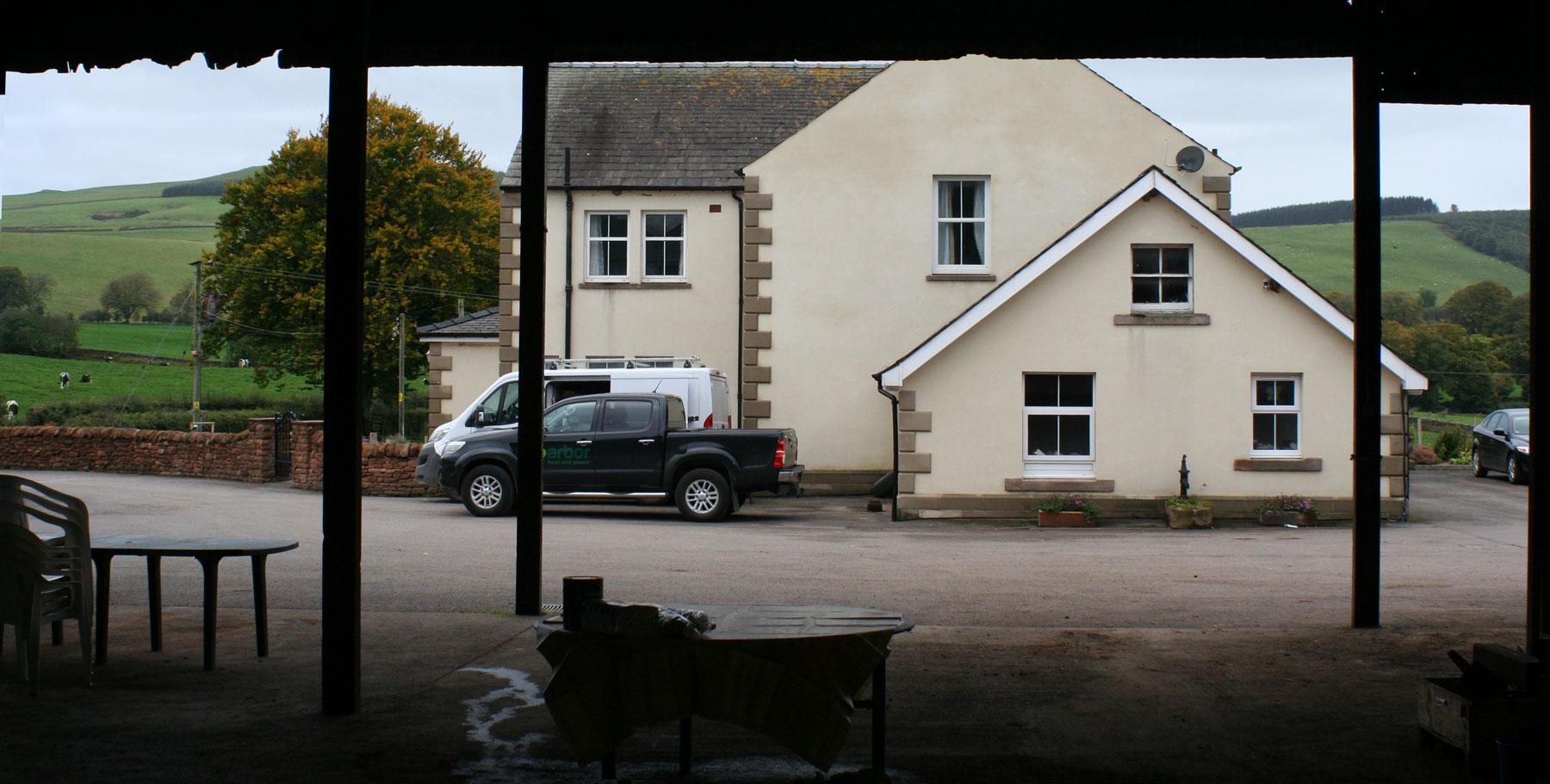
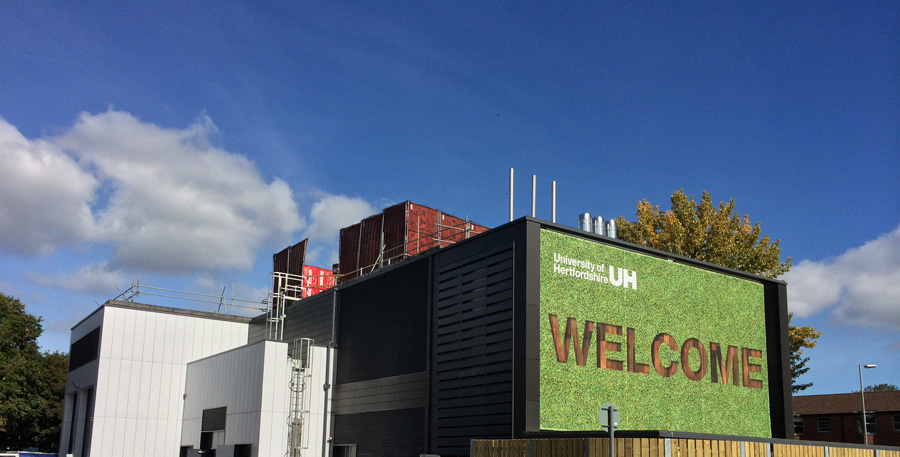
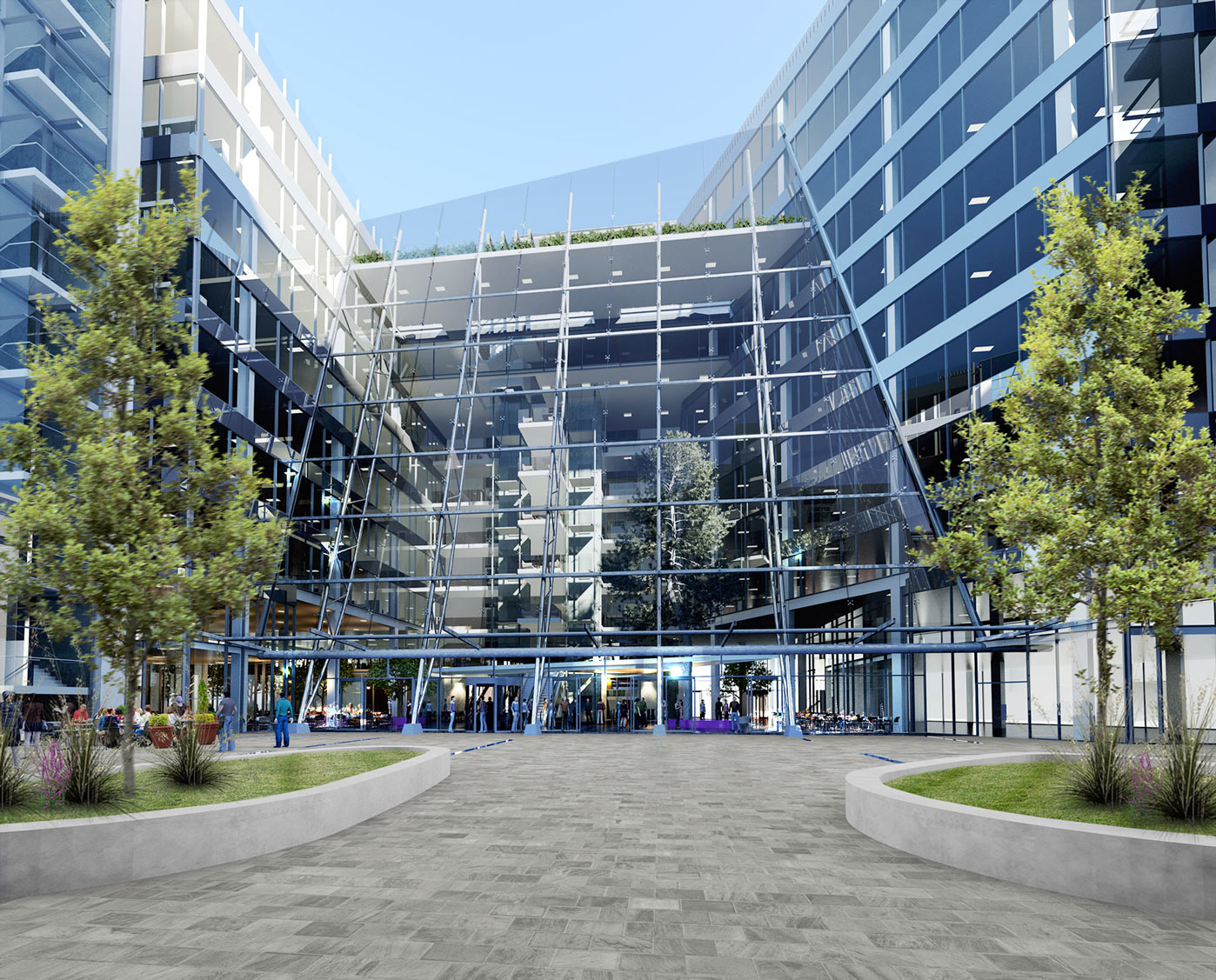
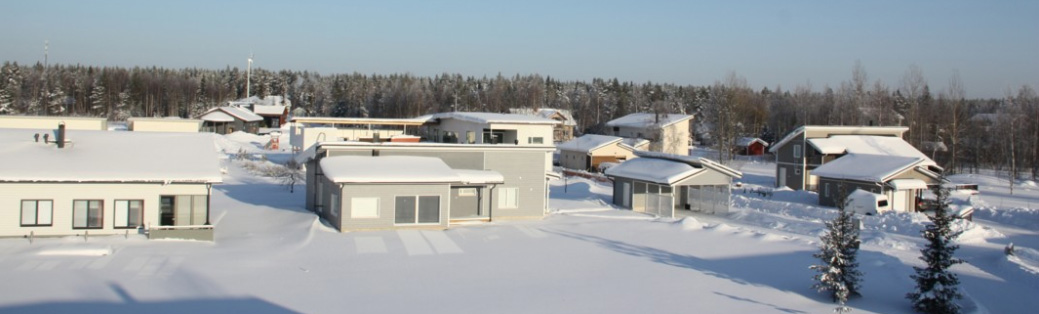